Electroless Nickel: How Low Can You Go?
Making Thin Electroless Nickel Deposits Work
When the thickness of any protective coating is reduced, two issues, porosity and chemical resistance, must be addressed. By looking at the whole picture, 1 micron of electroless nickel can provide the protection and low insertion loss required for 5G success.
IPC specification 4552 for ENIG lists the acceptable range for electroless nickel thickness as 3-6 microns or 118 to 236 micro-inches. This thickness range was developed mostly around rigid PCBs and definitely before 5G was available to the masses. It’s based on decades of history and billions and billions of PCBs successfully manufactured.
So why evaluate lower EN thickness?
The implementation of 5G increases signal speed and creates greater mobility. Higher speed requires lower insertion or signal loss and higher mobility requires a robust electrical connection. (Blog: “Thin High Phosphorus EN for 5G”) The dilemma is Electroless Nickel (EN) has a higher insertion loss and final finishes with low insertion loss do not provide the same reliability as ENIG or ENEPIG.
This dilemma has some OEMs looking at lower EN thickness but with 10.5% or higher phosphorus. High-phosphorus (10-12%) was chosen as that’s where EN becomes non-magnetic and non-magnetic metals have lower insertion loss1. Thin deposits decrease insertion loss. Also, a thin deposit has less impact on tight space requirements and improves flexibility. A couple of issues come up with thin EN deposits. The first is porosity, and the second is the chemical resistance of the deposit. Using high phosphorus EN improves chemical resistance but eliminating porosity in thin high phosphorus deposits requires a specialized formula.
Can porosity be eliminated with thin EN deposits?
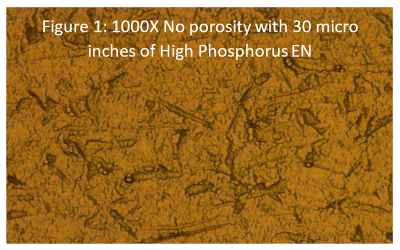
Yes, porosity can be eliminated, but getting there required looking at the entire picture to understand the causes for porosity. EN does not auto-initiate on copper and requires multiple steps to clean and seed the copper with palladium. The EN then initiates on the Pd seed sites and fills in between the sites as the nickel thickness builds. The two keys to eliminating porosity are ensuring good coverage of the Pd seed sites and control of the EN deposit. In this blog, we are going to focus on formulations to control EN deposition.
A high phosphorus EN bath further complicates porosity, as high phosphorus EN baths initiate and plate slower and typically require a higher thickness to fill the Pd seed sites. This can be overcome by using organic additives to force more lateral growth, therefore filling the Pd seed sites quicker and at a lower thickness (Figure 1).
What tests have been done to evaluate thin EN deposits?
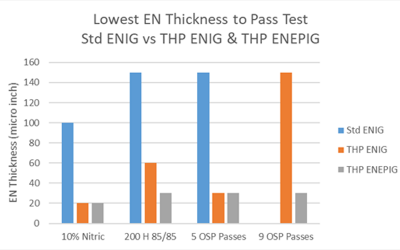
There are multiple tests with multiple variations being used in the industry to try to predict how a PCB final finish will perform in the real world. It’s nearly impossible to do every test variation. The following tests were chosen to evaluate the porosity of different thicknesses of high phosphorus EN. They are listed in order of least to most severe;
1. 30-minute immersion in 15% nitric with polysulfide indicator
2. 200 Hours 85oC/85% RH
3. Tape test after multiple passes through OSP pre-clean
We compared an ENIG with standard EN to a high phosphorus EN in both ENIG & ENEPIG applications. To compare these deposits, figure 2, shows the lowest thickness of each of these 3 deposits needed to pass each test. Standard ENIG with 150 micro inches could not pass the most difficult test, tape test after 9 OSP passes and needed a higher thickness to pass 15% nitric & 200 hours 85/85. ENIG with THP EN (Thin High Phosphorus Electroless Nickel) was able to pass all tests but required 60 micro inches to pass 200 hours 85/85 and 150 micro inches to pass 9 OSP cycles. ENEPIG with THP EN passes all tests with 30 micro inches of THP EN. THP EN does pass these tests with a lower thickness and can pass the most difficult test, 9 OSP passes, with 30 microinches when used in an ENEPIG deposit.
Performance of THP EN for soldering and gold wire bonding.
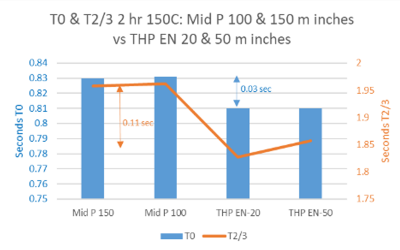
Wetting balance and through-hole soldering were used for comparison of typical EN to THP EN. Through-hole soldering was all 100%, whether THP EN or typical EN, with and without aging. All samples passed wetting balance and the curves all looked very similar. While there is not a lot of difference, even after aging, 20 micro inches of THP EN had a slightly lower time to zero and time to 2/3’s(Figure 3: 0.03 to 0.11 sec). From a solderability standpoint, this all indicates thin deposits of THP EN down to 20 micro-inches solders just as well as 150 micro inches of typical mid phosphorus EN.
Gold wire bonding was evaluated with 30 micro-inches of THP EN in an ENEPIG deposit. While the biggest impact to gold bonding is from the pure EP & immersion gold, we wanted to make sure changes in the base metal did not change the ability to gold bond. Just like soldering, using 30 micro inches of THP EN (Figure 4) performs just a well as 150 micro inches of mid-phosphorus EN.
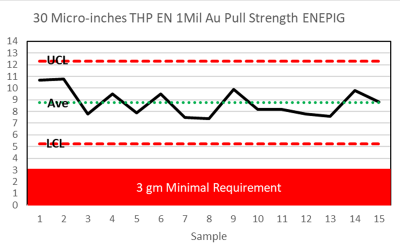
@ 30 micro inch
Based on testing, a THP EN deposit provides better protection but with no decrease in solderability and bondability. Also, testing for insertion loss discussed in an earlier blog “Thin High Phosphorus EN for 5G”2, shows THP EN reduces insertion loss by 50% over typical ENIG deposits. When you step back and look at the entire picture, THP EN with good lateral growth reduces signal loss and provides a deposit with high reliability. High reliability is certainly required for 5G implementation.
References
1: E Stafstrom, Introduction to D5810, Nov 2020
2: Technic PCB Blog, “Thin High Phosphorus Electroless Nickel for 5G Applications”
Author
Eric Stafstrom is currently the Global PCB Product Manager at Technic with over 40 years of experience in PCB fabrication and assembly.
Aggiungi un commento