Technic’s Black Knight - Graphite Direct Metallization Process
Introduction
Direct metallization systems based on conductive graphite are quickly gaining popularity throughout the world. The environmental and productivity gains that can be achieved with this process are outstanding. In today’s highly competitive and litigious environment, direct metallization reduces costs associated with compliance, waste treatment, and legal issues related to chemical exposure. Circudep Black Knight, Technic’s latest addition to our portfolio of advanced PCB processes, has been devised to address these needs.
In this blog, we will discuss what makes this graphite-based process a leader in the direct metallization space.
Why Use Graphite-based Direct Metallization?
Both carbon black and graphite-based chemistries are considered carbon-based, but there are significant differences between these two processes. The graphite process is based on a very fine and stable aqueous dispersion of synthetic crystalline graphite. The graphite particle, by virtue of its crystalline structure, is highly conductive compared to carbon black.
Graphite-based Black Knight is quite versatile in its ability to deposit graphite on non-conductive materials. This fact is especially important today, as the industry’s material suppliers push the envelope to produce higher performance resins and laminate composites. With each incremental enhancement in materials properties, such as CTE (coefficient of thermal expansion), Td (temperature of decomposition), signal integrity, and Tg (glass transition temperature), these materials become more difficult to process. These higher performance materials are highly cross-linked and more chemically resistant to processes such as alkaline permanganate desmear. Conventional electroless copper, by contrast, requires a micro-roughened resin surface to effect sufficient adhesion of the copper to the resin.
On the other hand, carbon-based systems are likened to a coating technology. Surface topography is not an issue for these systems to adhere to the resin materials. With respect to electroless copper, a precious metal catalyst (typically palladium) is required to bring about the oxidation of formaldehyde (the reducing agent most commonly used in electroless copper formulations). Essentially, electroless copper is composed of two half-cell reactions, with several process steps required to provide a void-free copper deposit. In addition, during the copper plating process, hydrogen gas has evolved. The production of hydrogen gas produces bubbles, which can lodge in small diameter through holes and blind vias. If the bubbles are not efficiently evacuated from the vias, plating voids will result.
The overall electroless copper reaction is shown below:
Overall Reaction: Cu(EDTA)2- + 2HCHO + 4OH- → Cu + H2 + H2O + 2CHOO- + EDTA4+
Environmental Advantages of Direct Metallization
Usually, the manufacturing cycle time to metallize a printed circuit board through a conventional electroless copper process is 45-55 minutes. Capex requirements aside, direct metallization offers faster throughput, which in turn reduces energy costs as well as greenhouse gas emissions. This is particularly important as sustainability concerns increasingly influence all manufacturing industries.
Water is an increasingly scarce commodity. The average electroless copper line uses 26-30 gallons of water per minute, versus 4-6 gallons per minute for a graphite-based process. Switching can generate an over 80% reduction in water consumption.
In addition, the graphite process does not contain chelated copper, which is used in conventional electroless copper. This greatly simplifies waste generation concerns.
Finally, Circudep Black Knight is free from formaldehyde, cyanide, and other toxic substances, satisfying the demand for safer, carcinogenic-free chemicals.
Black Knight is Ideally Suited for HDI and Flex Circuitry
With more emphasis on HDI and Ultra HDI, ease of use and speed are critical operational must-haves. Advanced Packaging is driving higher densities for both IC substrates, interposers and product boards.
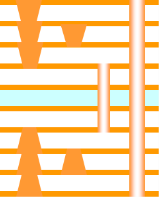
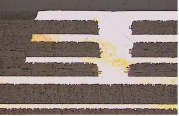
This necessitates the increased complexity of these boards and substrates with ever finer lines and spaces, multiple sequential laminations, and smaller diameter blind vias. Technic’s graphite-based direct metallization system is ideally suited for these challenges. The level of complexity is depicted in fig. 1.
In addition, the ELIC process (Every Layer Interconnect) is also practiced in the industry (fig. 2). With proper material selection, the constructions shown in fig. 1 and 2 will improve long-term reliability and withstand the multiple laminations required.
The key here is to select materials with low CTE and higher temperatures of decomposition.
The Black Knight direct metallization process enables faster productivity through primary metallization in contrast with conventional electroless copper.
The Science Behind Black Knight
The key element of Black Knight is the development of a unique dispersion of highly crystalline graphite particles in a slightly alkaline medium. The specific particle size of the graphite is engineered for a very narrow distribution range with diameter of 0.4-.-6 microns.
The use of proprietary dispersion agents and organic binders enhances the stability of the Black Knight graphite colloid. This in turn improves the adhesion and coverage of the graphite to a variety of materials including PPO, PPE, Liquid crystal polymer (LCP), flex, polyimide, PTFE, Ceramic filled materials, Via fill pastes, etc.
When discussing the consistency of colloidal graphite processes, the stability of the colloid is a major consideration. Stability is defined as:
1) Maintaining a consistent particle size without aggregation.
2) Particles remaining suspended in solution without settling.
Each definition of stability involves different factors and will be discussed separately. Our proprietary technology allows for the consistent graphite particle size and in turn enhances both the stability of the dispersion, and the excellent conductivity of the coating.
Consistent Particle Size
Colloidal graphite is a hydrophobic colloid, which means it is not strongly attracted to water. Hydrophobic colloidal particles are repelled from each other in two ways: sterically and electrostatically. Steric repulsion involves forming physical barriers to prevent the particles from aggregating. Electrostatic repulsion involves an electrostatic charge preventing the particles from coming into contact with each other and agglomerating. While both methods of repulsion are involved in keeping colloidal graphite particles from aggregating, electrostatic repulsion is of most interest due to the influence of contaminants on the electrostatic charges.
As previously stated, the graphite particle has a net negative charge. This negative charge is further increased by the addition of a proprietary binder, which at the operating pH also has a negative charge, due to the presence of carboxylate groups (R-COO-). Surrounding this particle is a cluster of counterions having a net positive charge. This unequal distribution of electrical charges sets up a potential across the interface and forms an electrical double layer. A schematic representation of this electrical double layer is shown in fig. 3.
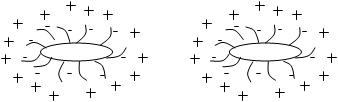
A thicker electrical double layer causes the particles to be repelled at a greater distance. This thickness is inversely proportional to the concentration and valence of each ionic contaminant. Therefore, ionic concentration should be reduced as much as possible, especially when the ion is divalent or trivalent. Zeta potential is a practical measure used to determine the effective charge on a colloidal particle. The more negative the zeta potential, the more stable the colloidal graphite dispersion. Zeta potential is also useful in evaluating the effect of contaminants on colloid stability. Our binder formulation helps to minimize the effect of contaminants that could negatively influence the stability of the graphite dispersion, and further negate the conductivity of the coating, once the coating is on the hole walls.
Importance of the Cleaner/conditioner
The cleaner conditioning process step precedes the graphite step in ensuring that the negatively charged graphite particles find a “home” on the various materials, including glass fibers. Again, the science behind this step is to match the positive charge imparted by the cleaner/conditioner to the negative charge on the graphite. This allows the graphite to “floc” to the vias and form a thin layer of conductive graphite on the glass and resin. This is actually a polymerization action forming a thin, conductive film on the non-conductive areas of the circuit board or substrate.
In conclusion, Circudep Black Knight offers numerous technical benefits compared to conventional electroless copper processes, eliminating potential issues associated with these systems:
- Improves the reliability essential for critical applications.
- Streamlines the process steps, leading to an overall reduction in costs.
- Offers environmental benefits, being free from toxic substances such as formaldehyde.
- Reduces water and energy usage due to longer processing times.
In addition to Circudep Black Knight, Technic supplies an expanding range of products and technologies to meet the demands of today’s PCB markets. Our R&D team will be happy to guide you through the selection or development of the specific process required by your application.
References
Direct Metallization System For Flexible Printed Circuit Board
Author
Mike Carano, PWB Final Finishes Consultant
Add new comment