5G and Creep Corrosion - Does it Matter?
The short answer is, yes. But, as always, it's never that simple or devastating. First off, what is Creep Corrosion? It’s the growth of copper sulfide crystals on a PCB surface that, as shown in figure 1 (SMT 2007 R. Schueller), can create an electrical short.
There are 4 conditions that must be present for this to occur;
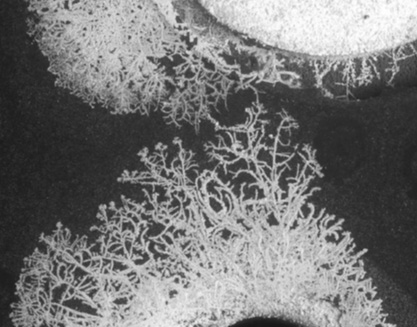
- Moisture (typically source is condensation).
- Acid - normally from flux residues but could be contamination left behind by the fabrication process or environmental exposure.
- Sulfur - typically from an industrial area or under the hood.
- Exposed Copper - porosity in a protective coating
The fourth factor, exposed copper, theoretically should not exist as copper is supposed to be encapsulated by a final finish to protect it. There have been a few papers published on this subject including “Creep Corrosion on Lead-Free Printed Circuit Boards in High Sulfur Environments” by R. Schueller (2007 SMTA). This paper identifies that the copper for this reaction is actually being removed from under the solder mask (figure 2, R.Schuller) for both SMT pads and through holes. Cu removal from under the solder mask was also reported by C. Xu et al from Alcatel-Lucent in 2009, “Creep Corrosion of PWB Final Finishes: It’s Cause and Prevention”. Xu’s work confirmed solder mask defined pads were prone to creep corrosion where, under the same conditions, isolated pads with no solder mask had no creep corrosion.
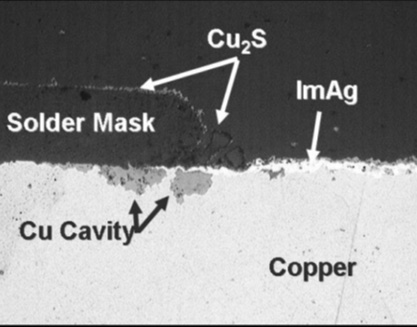
This work indicates PCB design influences creep corrosion. It’s not much of a stretch to understand that by impacting the solder mask-Cu interface, both solder mask processing and attack by the final finish process could impact creep corrosion. This was exasperated by early immersion silver processes that were very aggressive, attacking this interface as they scavenged for copper during the plating cycle. However, immersion silver has several advantages. We give immersion silver a more in-depth look in “Not All Immersions Silvers are Created Equal” as well as a planned future blog on “Fixing Immersion Silver for 5G”.
So why bring creep corrosion into a conversation about 5G?
First, final finishes that have the lowest impact on insertion loss are typically thin deposits of conductive metals like silver, palladium, or gold. These deposits have a difficult time passing more stringent aging requirements like HTHH, fuming nitric acid, and or neutral salt spray. This indicates there is more porosity and since there is no barrier metal, there is little resistance to copper migration. This is a major reason ENIG and ENEPIG are used on high-reliability products even though EN has almost 2x more insertion loss.
It’s been reported for years that nickel has a high insertion loss due to low conductivity and its magnetic nature. One solution, especially for the immediate future of 5G, is a thin deposit of high phosphorus electroless nickel. Magnetism in electroless nickel goes to 0 as the % phosphorus approaches 10.5%. As shown in figure 3, work done with Rogers Corporation shows that insertion loss is almost cut in half with thin, high phosphorus electroless nickel. But you have to look at the whole picture as insertion loss is just as important as being able to pass the more difficult aging requirements using a thin deposit. To do both requires a specialized 5G electroless nickel with good lateral growth.
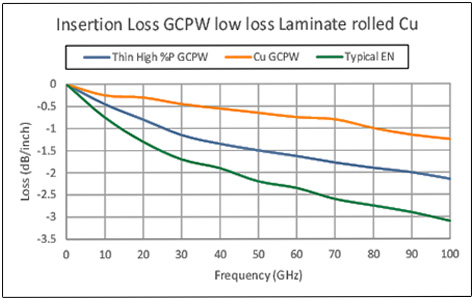
The second main reason to be concerned about creep corrosion is that 5G opens up huge opportunities for increased mobility. This mobility will expose electronics to environments more prone to condensation and, therefore, increases opportunities for creep corrosion. In either cold or hot humid climates, electronics will be exposed to condensation as they move back and forth from a controlled office or home environment to the outdoor ambient environment. Condensation is one of the 4 driving forces needed to create creep corrosion and, with 5G, there will definitely be more opportunities for condensation to form.
Potential for creep corrosion will increase with under the hood automotive applications. Also, with mass autonomous transportation on the horizon, reliability becomes paramount. Until everyone, including large diesel transports, goes electric, not only will we have condensation but we will also have a corrosive environment with higher sulfur levels. Finally, mobility adds another factor, increased human contact. This contact increases exposure to corrosive sweat & fingerprint oils as well as the mistakes that all humans make.
What’s the solution?
We started this discussion by stating creep corrosion does not have one simple answer and, so far, there have been no reports of devastating field failures due to creep corrosion and 5G implementation. But all the elements to make creep corrosion an issue are beginning to move into place as we transition further into 5G implementation.
- Thin 5G Final Finishes that are susceptible to creep corrosion
- Increased contact with condensation due to increased mobility
- Increased use in high sulfur environments
- Presence of corrosive soldering materials and atmospheres
Today there are “5G Final Finishes” like EPIG, EPAG, IS, ISIG that meet the low insertion loss requirements for 5G but cannot provide the protection for high-reliability applications that ENIG & ENEPIG can. An interim solution is to use a thin, high phosphorus electroless nickel to lower insertion loss and still pass the more difficult reliability tests. This finish is also solderable, bondable, and provides low contact resistance. Improvements to finishes like EPIG and immersion silver to make them more robust are being formulated, but it will take time to develop these processes and for them to gain acceptance.
Unfortunately, there is no one switch to flip that will completely eliminate every concern of experiencing creep corrosion. Just remember to always look at the whole picture.
References
1: R. Schueller, Creep Corrosion on Lead-Free Printed Circuit Boards in High Sulfur Environments, 2007 SMTA
2: E Stafstrom, Introduction to D5810, Nov 2020
Author
Eric Stafstrom is currently the Global PCB Product Manager at Technic with over 40 years of experience in PCB fabrication and assembly.
Add new comment