Increased demands on reliability result in the implementation of more stringent requirements
One of the major functions of electroplated coatings is to increase the corrosion resistance of the substrate, such as the primary copper in circuit boards and connectors, or other layers onto which the coating is applied. In electronic applications, these coatings are also required to impart specified electrical conductivity and wear resistance. Furthermore, the coating must enable attachment to other surfaces via soldering, physical insertion, etc.
New regimens, such as 5G communications, miniaturization, or consumer applications requiring nickel-free and sweat-resistant deposits, continue to give rise to challenges in electronic finishes. The purpose of this article is to review some of these trends, featuring how Technic's leading solutions can satisfy emerging requirements in connector applications.
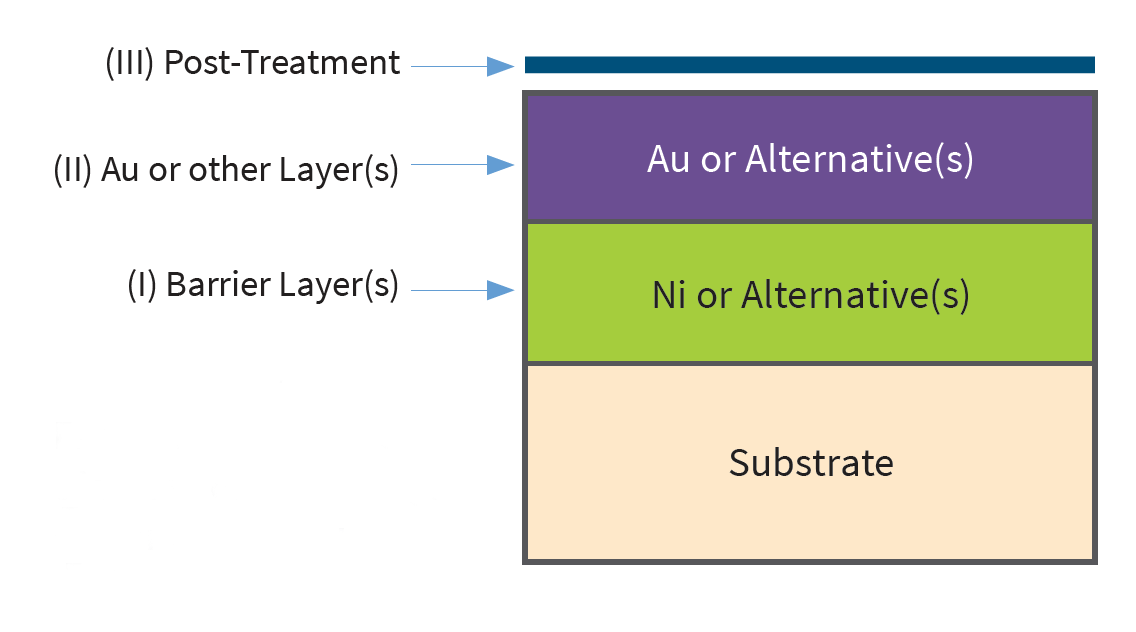
The industry standard of conventional electroplated nickel (1 to 2 μm) plus hard gold (0.10 to 0.75 μm, depending on the application) has served many portions of the electronics plating industry well for several decades. As shown in fig. 1, the nickel provides a barrier layer to protect the copper substrate, which would otherwise tarnish, rendering it unusable. The gold layer provides enhanced conductivity, wear resistance, and solderability, whereas the post-treatment protects the underlying layers and preserves solderability in storage.
However, increasing demands on reliability has resulted in the implementation of more stringent requirements, particularly concerning corrosion protection. In addition, as integrated circuit (IC) semiconductor devices and printed circuit board (PCB) dimensions have been scaled down, the geometric demands on electronic interconnects have increased dramatically. Hence, the development of more robust alternatives to the nickel/gold system has become essential.
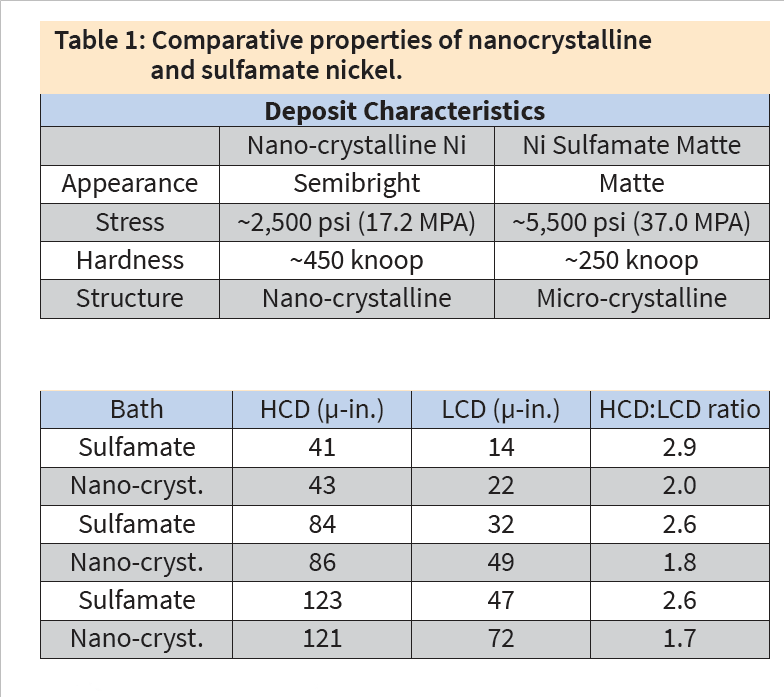
Improved Barrier Layers
The traditional barrier layer for electronics finishes is matte nickel sulfamate. This process has served the industry well over the years, but miniaturization and increased geometric complexities have presented challenges that exceed the coating’s limits.
Technic’s Techniphos 615 is particularly effective as a barrier layer in electronic connector plating applications, especially for those applications requiring an electrolytic nickel-phosphorous deposit, as well as in applications requiring a low degree of magnetism. Techniphos 615 is an electrolytic nickel/phosphorous alloy, capable of plating high phosphorous-containing deposits over a wide current density range.
For applications where pure nickel must be maintained, the Goldeneye Nickel process has been developed. This nanocrystalline nickel electroplating process has been engineered to improve nickel thickness distribution and corrosion resistance from a proprietary electrolyte in high-speed/reel-to-reel plating applications.
The grain size of the semi-bright, low stress and ductile deposits yielded by this process is on a nanoscale, approaching an amorphous deposit. Comparative properties are shown in fig. 2 for the nanocrystalline and sulfamate nickel deposits. The higher solution conductivity suggests improved throwing power. This is borne out by the data for the connector design shown in fig. 2, where the thickness distribution is improved by 30-40% with the use of nanocrystalline nickel.
Goldeneye Nickel BF provides all the advantages of Goldeneye Nickel, with the added value of being a boron-free electrolyte. Among the safety, environmental and performance advantages of Goldeneye Nickel BF is its ability to operate without the formation of boric acid crystals in the bath and on the equipment.
Alternatives To Gold/Post-treatment Processes
The search for alternatives to gold plating is often cost-motivated. However, innovative technologies aimed at reducing or replacing gold usage, while enhancing environmental compatibility, operational safety and performance, are also key drivers in new product development.
Currently one of the more promising alternatives is the use of silver with an appropriate post-treatment. Until today, two technical issues have limited silver’s implementation in non-automotive applications:
- Wear resistance, especially after multiple insertion cycles.
- Corrosion resistance, such as overcoming the silver tarnish issue.
The automotive use of silver is currently restricted to sealed applications with minimal insertions. An ideal solution would be a wear-resistant/corrosion-resistant silver plating process. Conventional silver, however, exhibits a high friction coefficient of about 1.2, as plated and after baking. For applications requiring superior corrosion resistance, Technic supplies a proprietary two-part system for silver alloy plating, consisting of a silver alloy electroplated deposit with Durasil® Silver, followed by a unique post-treatment process chemistry, called Techniseal Ag.
Durasil® Silver is a proprietary silver alloy plating process, designed to replace gold in reel-to-reel electronic component and connector applications. It provides excellent conductivity, superior corrosion resistance, and improved wear resistance compared to conventional silver plating processes.
Techniseal Ag is a powerful, electrolytic silver anti-tarnish process that deposits a nano-scale coating on the surface of the silver deposit.
Key advantages of using Techniseal Ag include:
- It passes sulfur corrosion testing, consisting of a full immersion of parts in a 5% potassium sulfide (K2S) solution for five minutes. Similar results were observed with five days of MFG exposure per EIA-364-65B, Class IIa.
- It works for both high-temperature protection, as well as sulfur corrosion protection, a unique characteristic compared to other post-treatment chemistries that can only work for one or the other.
- It does not negatively affect contact resistance and is completely free of chrome compounds.
In summary, several options may be considered when it comes to silver plating, depending on specific customer requirements. As we have just seen, silver alloy plating followed by post-treatment may be an option, but also silver plating with a nanocoating for corrosion protection only, or even silver plating with a two-step, post-treatment process sequence consisting of a nanocoating plus post-dip (lube), may be more effective for some applications.
Emerging Applications Require New Finishes
As new applications emerge, the electronics finishing field continues to be presented with new challenges. Significant among these are electrolytic, sweat-resistant connector finishes required in the mobile phone arena, press-fit connector pins, and 5G applications.
Two changes in cell phone technology have had a major impact on the plated finishes used for mobile phone connectors. The first is the replacement of the traditional headphone jack with a single connector that performs both the electrical charging function and the headphone connection. The second is the implementation of “quick-charge” connector technology. When mobile phones first became common, conventional charging involved a 5 voltV/1 amp or 1.0-watt charge regimen. Through three generations of “quick-charge” development, dynamic charging, involving up to 18 watts are common today.
Both of these factors have affected mobile phone connector technology. Consumers exercise while using headphones and/or charging their cell phones, thus handling the connector itself, resulting in human sweat being present on the plated connector in the presence of electrical current.
The introduction of connector press-fit pin applications has led to new developments. The use of matte tin plate in these applications has resulted in extremely long whiskers under certain press-fit conditions; whiskers can create short circuits. Fast growth of whiskers is observed in press-fit connections because of high mechanical stress at the pure tin surfaces.
Connector companies and end users have been experimenting with various non-tin solutions for years. Recently, a number of alternative finishes have emerged as potential solutions for press-fit pin whiskers formed under compression. Tin alloys (Sn-Ag, Sn-Bi, Sn-Pb) over nickel have shown promise, but a tin-free layer of indium has shown significant performance improvement.
Techni Indium HS is an indium electroplating process designed for use in the selective plating of press-fit pin connectors, in order to prevent the formation of harmful metallic whiskers. After extensive in-house and field testing, this electrolyte has proven to be very robust, with exceptionally whisker-resistant deposits. The current density range of the process is extremely wide – 50 ASF to 250 ASF – with relatively low metal concentrations in the electrolyte. Another key advantage of this product is that, unlike competitive processes, there is no need for an indium strike when plating over nickel, which will effectively minimize costs.
Another challenge in electronic finishes is posed by 5G communications and attendant high frequencies rapidly coming online. In this case, it has been found that the design of the PCB final finish must take high-frequency signal loss into account. Additional high-frequency signal loss is encountered with the presence of the standard electroless nickel/immersion gold (ENIG) system, with the nickel deposit being the primary source of this signal loss.
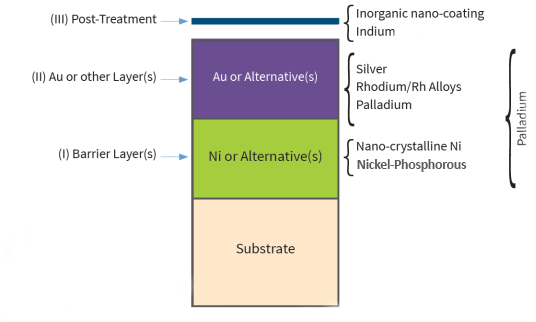
Studies have shown that the connector finish necessary to minimize signal loss requires a nickel-free barrier layer, plus good conductivity and corrosion resistance for the final finish. Palladium is a suitable deposit that can function as both a barrier layer and a final finish. However, barrier layer effectiveness requires a high thickness (>0.75-1.0 μm), and electroplated palladium is known for microcracking at high thicknesses.
A potential solution to this problem may be a proprietary microcrack-free palladium process, called Pallaspeed 990. This process is a chloride-free, low ammonia palladium plating solution, designed to produce highly ductile palladium deposits and achieve exceptional corrosion and wear resistance. Pallaspeed 990 produces low-stress deposits, with no spontaneous microcracking observed up to a palladium thickness of 4 μm. Thicknesses of up to 2 μm resist cracking during bending. The process operates at a neutral pH and exhibits no ammonia smell. It is a stable electrolyte with a wide current density range.
In conclusion, rapid and continuous changes are occurring in the electronics finishing field. As a result, alternative finishes to the conventional Ni/Au are being considered to meet new requirements, including materials that were never before considered feasible in connector applications (fig. 3). As additional changes will continue to occur, connector finish technologies need to keep up with the demands of other interconnects, as well as use environments.
In addition to those described in this blog article, Technic supplies a wider range of products and technologies to meet the demands of today’s connector markets. Our R&D team will be happy to guide you through the selection or development of the specific process required by your application.
References
M. Myers, “Overview of the Use of Silver in Connector Applications”, Tyco Electronics Technical Paper 503-1016, 5 February 2009.
Dr. H-P Tranitz, “Whiskers and Alternative Surface Finishes at Press-in Technology”, IPC APEX EXPO, 18 Feb. 2012, San Diego, CA, USA.
J. Coonrod, “Ambiguous Influences Affecting Insertion Loss of Microwave Printed Circuit Boards [Application Notes]”, July 2012, IEEE Microwave Magazine 13(5):66-75
R. Schetty, Next-Gen Corrosion-Resistant Finishes for Electronics, September 2019, Products Finishing, PFonline.com.
Author: Rob Schetty is the VP of Technology, Sales, and Marketing at Technic.